Tim O'Brien® Homes and BASF join forces to create the future of home building. Working collaboratively, the experts at the BASF Center for Building Excellence and the team at Tim O'Brien Homes were able to effectively evaluate costs and systems on the home, and ultimately, optimize the value for the builder and customer alike.
A High Performance Partnership
At Tim O'Brien Homes, green building is a critical part of the successful builder's on-going commitment to improving their homebuilding process, and has resulted in more energy-efficient, durable and comfortable homes.
Recently, the Wisconsin-based builder looked to leading chemical company BASF to help take another giant leap in its commitment to continuous improvement. "The idea that a $100 billion company recognized for advancing building science expertise and innovations in construction chemistry was offering to help us improve our processes through a top-to-bottom, hands-on consultation was very attractive," said Tim O'Brien, president of Tim O'Brien Homes.
A team of building scientists, architects, engineers and sustainable construction experts from the BASF Center for Building Excellence was assembled and immediately put BASF's BEYOND.High Performance®approach to work. "Leveraging our comprehensive HP+™ Consultative Solutions, we were able to get a more holistic view that would allow us to effectively address the specific needs of this particular builder and this particular opportunity," recalled Rick Davenport, director of sustainable construction for the BASF Center for Building Excellence.
Architectural designer Emily Van Court, Associate AIA, SEED, and Home Energy Rating System® (HERS) Designated Associate, led the team. "It's all about what the builder needs and cares about, and what their performance targets are on a particular project," noted Van Court.
"We appreciated that BASF spent time with us to learn how we build homes before ever discussing potential recommendations for improving our building envelope," stated Craig North, Tim O'Brien Homes, director of construction.
Together, the BASF and Tim O'Brien Homes teams analyzed everything from the orientation of the home, to advanced framing techniques, to mechanical strategies and more. "We're committed to the building science details, especially moisture management, indoor air quality and thermal bridging," said North. "And BASF's expertise in that regard was critical."
"BASF's team brought a variety of different skill sets to the table," O'Brien recalled. "All those disciplines working together really made this work and kept the process moving.".
Implementing Innovation
In order to develop a fully integrated program, we first analyzed their existing build process. Among the most critical components was the builder's participation in the HP+™ Wall System trial, which featured advanced framing and incorporated four control layers in a single wall design to deliver integrated control of heat, air, moisture and vapor flow.
"Before implementation, we met with the trade partners to inform them of the plans and what each change meant to individual areas," recalled Van Court. "This helped everyone to understand all of the interconnecting pieces and new processes."
Joining Van Court at the meeting from BASF was Jamie Hicks, Registered Architect, LEED® Accredited Professional BD+C, CDT Construction Documents Technologist. His strong working knowledge of construction helped Tim O'Brien Homes throughout implementation.
"Jamie was on-site, literally tool belt on," said North. "He really helped us understand some of the new processes, met with our trade partners, and made sure everything was done properly the first time.
Results
Through the implementation of BASF's BEYOND.High Performance approach and its HP+ Wall System, the home achieved a significantly lower HERS score. The process also enabled the builder to allocate costs in an extremely efficient manner, in some areas reducing both materials and labor. Plus, since the HP+ Wall System's design capacity has been demonstrated to be 35%* greater than the design capacity of a wall built with standard framing and OSB with full sheathing, its installation also positively impacted the home's structural integrity.
*HP+ Wall System calculations are based on AWC Special Design Provisions - Wind and Seismic (SDPWS), Section 4.3; Equations were derived from ASTM E2126 testing. OSB wall calculations are based on AWC Special Design Provisions - Wind and Seismic (SDPWS), Section 4.3. Results may vary depending on wall configuration.
BASF HP+ Consultative Solution
Learn how BASF engages with builders to develop a forward plan on how to improve building processes in this video
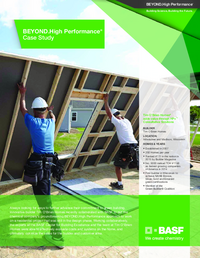