This article was published by Wells Concrete (link below) who is soley responsible for its content. Because of this, BASF can not vouch for the validity of any facts, claims or opinions in the article. The story is being rebroadcast here to simply raise awareness.
Step I: Layout
First the lengths and the widths of the pieces need to be laid out and set up. This is done on one of our prestressed forms, our forms have hydraulic side rails-which make it more efficient when it comes time to remove the forms! Once they are set, any other opening-window, service door, etc will be laid out as well and put in the panel.
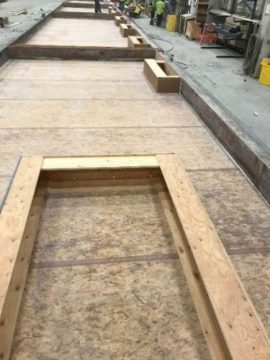
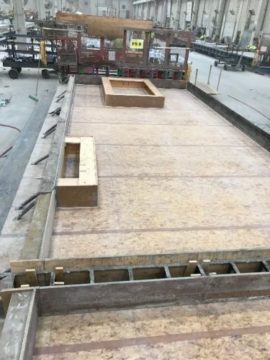
Step II: Strand and Reinforcement
Once all the overall measurements are set and openings are in, the form will be oiled and then strand pulled, and then tensioned. Following tensioning, all of the reinforcement-rebar-will be added and tied in for that layer.
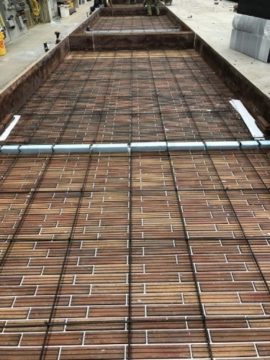
Step III: Pouring and Insulating
After all the rebar is added and tied in, the architectural concrete can be poured. Once it is poured, it will first be screeded off and then vibrated to ensure proper height and consolidation. After this is complete, insulation will be added and wythe connectors will be-this is down to ensure the panel with hold together.
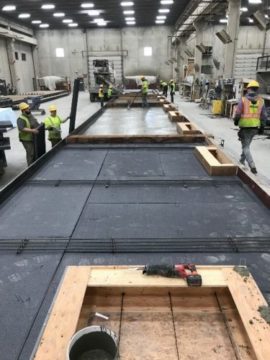
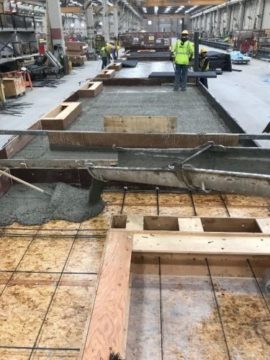
Step IV: Structural Reinforcement
Before the structural concrete can be added to the panel, all the structural reinforcement must be added, and an additional layer of strand. The strand will be tensioned, just like in the architectural layer, and then all reinforcement will be tied in.
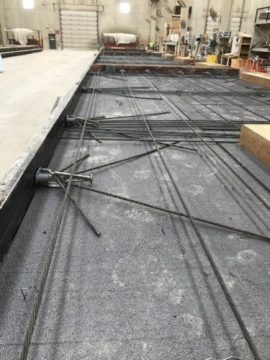
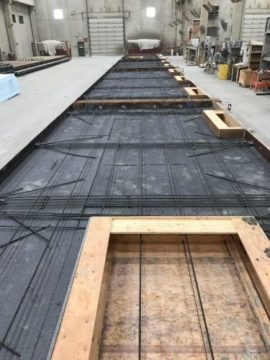
Step V: Pouring and Finishing
After all reinforcement is tied in, a structural mix can be poured to finish the panel. This concrete will be screeded and vibrated-similar to the architectural layer, then any screed face plates can be added. After all plates are added, the concrete can be finished to any desired level.
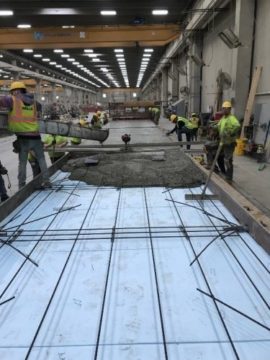
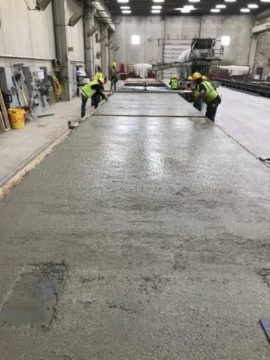
Matt Everding
Wells Concrete | Director of Operations